Accelerating Hydrogen Storage with Low-Cost Alkaline Electrolyzers
Posted on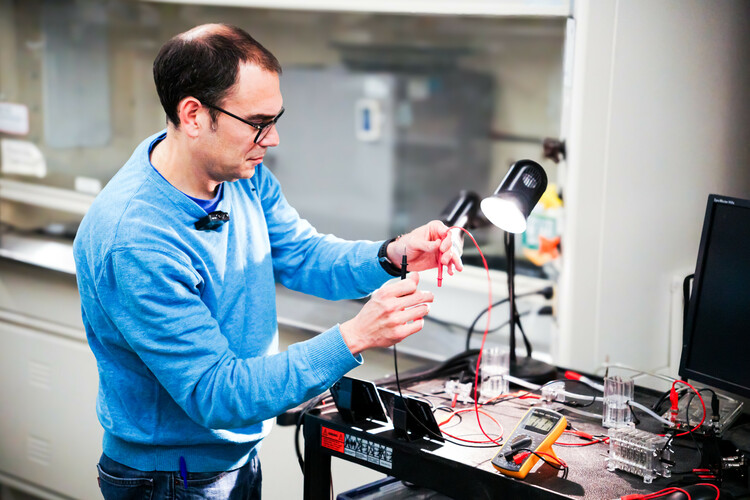
Dr. Marc Secanell simulating hydrogen generation.
The future of renewable energy depends on more than just generating renewable electricity from the sun and wind. It depends equally on how well we can store that energy when the weather changes or the grid is under pressure. In the Energy Systems Design Lab (ESDL) at the University of Alberta, Dr. Marc Secanell and his team are working on exactly that. They're building next-generation energy carrier systems that are reliable, scalable, and sustainable.
As a professor in the Department of Mechanical Engineering, Marc has spent his career designing and developing electrochemical systems like fuel cells, electrolyzers, and batteries. Currently, the challenge for him is to push their work beyond lab-scale success to create hydrogen systems that are viable for a planet of eight billion people.
“One thing working in a lab has taught me is that just because something works once doesn’t mean it’s ready for the real world. I can do something one time in the lab. But if we want it to work for everyone, it has to work 150 times and it has to work 150 times cheaply, with materials that are sustainable.”
The ESDL specializes in combining experimental work with simulation to improve electrochemical systems that store and convert energy. Right now, the team is focused on alkaline-based electrolyzers, a device that can split water into hydrogen and oxygen using electricity from renewable resources: “Hydrogen isn’t new," Marc explains. "People were talking about offshore wind powering electrolyzers as far back as the 1960s. The difference now is in the detail, how to make the system durable, affordable, and scalable."
Rethinking Electrolyzers with Alkaline Exchange Membranes
Today, many commercial hydrogen systems rely on proton exchange membranes (PEMs) that require rare, expensive metals like iridium and platinum. As demand grows, access to and sourcing these expensive materials can bottleneck the ability to globally adopt this technology at scale. For Marc, the solution lies in revisiting an older technology with new materials, such as the alkaline exchange membranes (AEM) electrolyzers.
Alkaline electrolyzers have been around for decades, but were previously limited by membrane technology. Recently, new membranes capable of transporting hydrogen ions (OH-) have opened new potential, and working closely with companies like Canadian startup Ionomr, the ESDL team is integrating this technology into working systems.
Designing a better system isn’t just about swapping materials. It’s also about rethinking the architecture of the electrolyzer itself. But Marc’s lab doesn’t build the entire electrolyzer stack. Instead, they focus on the smallest, most critical component—the catalyst layer, or the space between two electrodes, where the majority of energy loss occurs: "If you can improve performance in just one cell, that improvement can then get multiplied across every cell in the system, sometimes up to hundreds of times," Marc explains.
To make these improvements, the lab uses inkjet printing to create precise, high-performing electrodes with custom-formulated catalyst inks. Inkjet printing uses isolated droplets, reducing health risks for researchers working in the lab. Though a slower process than conventional methods, this approach wastes far less material and also offers the researchers more control.
“Most labs use grams of catalysts,” Marc says. “With inkjet printing, we use milligrams. We mix our own inks, test their particle sizes and viscosities, and print them drop by drop. The approach is not only efficient but is also safer compared to traditional spray methods that can release airborne nanoparticles."
The added level of control also allows the team to experiment with functional gradient electrodes. This streamlined process allows the team to print different catalysts for different parts of a single electrode. More control also means the ESDL team can shape electrodes to match specific flow channel designs.
Building Systems that Scale
Marc’s work is rooted in the belief that successful energy technologies must be both technically sound and globally scalable. That means designing systems with economic viability, material availability, and political realities in mind.
“There’s always this tension in energy research. Everyone wants to save the environment, but there are always competing interests,” he shares. “So, this duality is painful because then it can become challenging to frame your research and think about the bigger picture.”
To navigate this challenge, the lab relies on an interdisciplinary team. They collaborate with national and international partners to get that bigger picture. Partners include the National Research Council of Canada, Fraunhofer Institute in Germany, and industry leaders like Sunfire, along with additive manufacturing experts such as Dr. Ahmed Qureshi at the University of Alberta. Together, they bring the expertise needed to develop each component of a fully-functioning electrolyzer system, from ink formulation and membrane testing to device integration and scaling.
Despite balancing technical challenges and broader economic questions, Marc is optimistic about future possibilities when research is grounded in both scientific detail and practical purpose: “The devil is in the details,” Marc emphasizes. “We get the materials, the process, and the design right. Then, we will be ready for what's next."
Watch Dr. Marc Secanell’s interview with Future Energy Systems on YouTube: Storing Energy With Hydrogen Using Low-Cost Alkaline-based Electrolyzers | Accelerator Project
This story is part of Future Energy System’s Accelerator Project Series. For more information on the Accelerator Projects, click here. To stay up to date with this series, subscribe to our monthly newsletter and follow FES on social media.
Further Reading:
Energy Systems Design Laboratory (ESDLab)
Using Additive Manufacturing to Fabricate Non-precious Metal Electrodes for Water Electrolysis