Playing with fire: deposition processes for multi-functional coatings
Posted on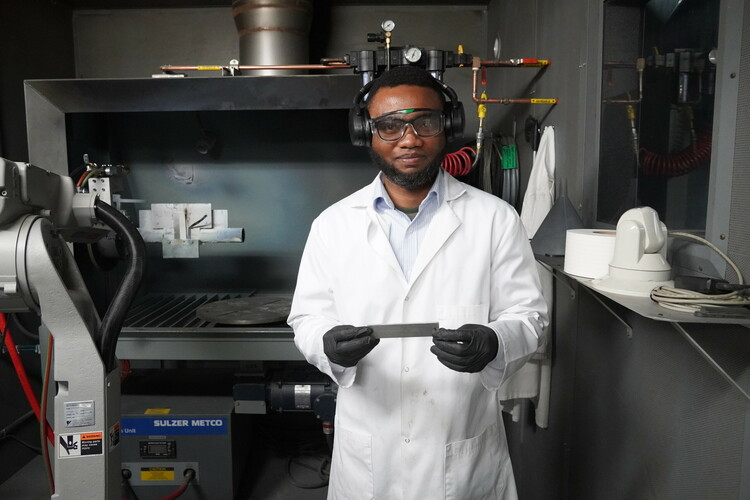
Research Assistant and PhD Candidate Adekunle Ogunbadejo presents a substrate sample in front of thermal spray equipment
Dr. André McDonald began researching the fabrication, development, and performance assessment of thermal and cold spray coatings nearly 20 years ago. Today, his research focuses on developing multi-functional coatings that provide wear and erosion resistance and heat protection. He’s also focusing on the utilization of these functionalized thermal-sprayed coatings in industrial applications such as de-icing of structures under cryogenic conditions, performance testing of wildfire chemicals with custom-made sensors, and performance of building equipment systems. The coatings also leverage sensors that can monitor the health of a variety of structures by leveraging machine learning artificial intelligence.
About the technology
Dr. McDonald’s research group has been working with different coating types that are composed of a single element, alloy, or compound with unique physical properties.
The group works with metallic and ceramic coatings. Metallic coatings can be composed of a single element, but recently the group has been working on the development and testing of High Entropy Alloy (HEA) coatings composed of five equi-atomic elements. When applied, these coatings—which are a new class of advanced metallic materials—provide protection and increase the lifespan of wind turbine blades, helicopter blades, and metal pipes.
Conversely, ‘ceramic’ means any material that is nonmetallic and non-organic, such as aluminum oxide (alumina) or silicon dioxide (silica). These coatings insulate and protect structures. In Alberta, one application is protecting pipes with heated coatings to prevent oil transport from slowing down in cold winter temperatures. A third type of coating, metal matrix composites, or MMC, can be either a ceramic coating containing metallic particles, or a metallic coating containing ceramic particles.
How are the coatings applied?
The coatings are deposited via two methods in this research—one uses a pressure-drive cold spray and the other through a flame spray process. For the cold spray method, the coating is applied using compressed air. This is a kinetic process, similar to a pressure washer or an extremely high-pressurized spray paint can. Since this method is highly pressurized, the process relies on plastic deformation of the materials the coatings are deposited on. The cold pressure spray technique is engineered to deposit the coatings at low temperatures, below the melting point of the coating. Flame sprays, however, have a more complex procedure that is carried out at a much higher temperature in an oxy-acetylene combustion process.
There are three general steps to successfully depositing the coatings with flame spray. Research Manager Dr. Ophelia Jarligo walked us through the process: “First, we prepare the substrates. There must be an anchor for the coating to stick to, so the surface must be roughened a little bit.”
Erosion agents are used to roughen up the surfaces during a process called grit-blasting. The eroded surface can then act as a sort of Velcro for the coatings to stick to. The grit-blasting is done in the enclosed chamber to prevent the hard particles that are used for the grit-blasting from hitting the operator of the equipment, since they move at very high speeds. This is also to keep the dust, resulting from the impingement process enclosed, as much as possible. Before the coating is applied, solvents are applied to the substrate to clean off any excess dust.
The final step is depositing the coating using flame spray. This is done with a flame gun on the end of a mechanical arm, which is pre-programmed and controlled from outside of the blasting area. During the application, a combustion process heats up gas to produce a high-temperature flame, partially melting the feedstock surface and resulting in metallurgical bonding. Watch a coating deposition with the flame spray process below.
So, what’s the difference between cold and flame sprays?
Simply, cold sprays do not require the combustion of gasses to work and the process results in a mechanical bond. This makes the cold spray process preferable over the flame spray if the composition of the desired coating is the same as the starting material. Since flame spray results in a metallurgical bond, the chemical composition of the coatings can vary from the feedstock material.
Although the cold spray is a more accessible option, they’re less effective for ceramic coatings, which are less ductile and would take much larger amounts of kinetic energy to adhere properly. Certain ceramic feedstocks can be engineered to adhere to substrates with the kinetic process, but overall, the flame spray is a more effective way to deposit ceramic coatings.
Future directions
Looking forward, the research group has a few different plans for thermal spray technology. To incorporate sustainability into the research, Dr. McDonald has been substituting rare critical elements for earth-abundant metals.
They’re also currently working with researchers from the mechanical engineering department to develop an autonomous cold spray manufacturing and repairing process.
“The biggest challenge is ventilation,” Dr. Ophelia Jarligo explains. “We have specially designed dust collectors in an enclosed area that allow us to run this process safely without having to worry about particles being released into the atmosphere.” Despite this challenge, they’re optimistic that they’ll have the prototype working in no time.
Another area the group is expanding into is the hydrogen economy. The coatings function well for the transportation and storage of hydrogen because they protect the pipes and container tanks from embrittlement.
“We’re already working with industry partners like Cenovus to demonstrate the usefulness of this technology,” Dr. McDonald adds. “This will continue work on establishing low-carbon energy generation methods to get us to that net-zero target.”
This research project was partially funded by the Joint Booster Program between the University of Alberta and the University of Calgary. To read more about the program or apply for funding, check out our article here.
Dr. André McDonald is currently the Associate Vice President (Strategic Research Initiatives and Performance) and a Professor in the Department of Mechanical Engineering at the University of Alberta. He received his BSME in 2001 and his MSME in 2002 from the City College of New York. He was awarded his Ph.D. from the University of Toronto in 2007. Read more about Dr. McDonald here.